What is Porosity in Welding: Secret Elements and Their Effect On Weld High Quality
What is Porosity in Welding: Secret Elements and Their Effect On Weld High Quality
Blog Article
Recognizing Porosity in Welding: Checking Out Causes, Effects, and Prevention Methods
As experts in the welding market are well aware, recognizing the reasons, results, and prevention techniques related to porosity is critical for achieving durable and trusted welds. By delving into the root creates of porosity, examining its damaging results on weld quality, and checking out reliable avoidance strategies, welders can improve their understanding and skills to generate high-quality welds regularly.
Common Reasons of Porosity
Porosity in welding is largely created by a mix of elements such as contamination, inappropriate shielding, and poor gas coverage throughout the welding procedure. Contamination, in the kind of dirt, grease, or corrosion on the welding surface area, develops gas pockets when heated up, causing porosity in the weld. Incorrect shielding happens when the securing gas, commonly used in processes like MIG and TIG welding, is incapable to completely protect the liquified weld swimming pool from responding with the bordering air, resulting in gas entrapment and subsequent porosity. Additionally, insufficient gas coverage, frequently because of incorrect circulation prices or nozzle positioning, can leave components of the weld unguarded, permitting porosity to create. These factors jointly add to the development of voids within the weld, deteriorating its integrity and potentially creating architectural problems. Recognizing and addressing these usual causes are vital steps in stopping porosity and ensuring the top quality and toughness of bonded joints.
Results on Weld Top Quality
The existence of porosity in a weld can substantially jeopardize the overall quality and integrity of the welded joint. Porosity within a weld produces spaces or cavities that deteriorate the structure, making it a lot more susceptible to fracturing, deterioration, and mechanical failure. These voids act as anxiety concentrators, lowering the load-bearing capacity of the weld and raising the probability of premature failing under applied anxiety. Additionally, porosity can also act as prospective sites for hydrogen entrapment, more worsening the destruction of the weld's mechanical properties.
Moreover, porosity can impede the efficiency of non-destructive screening (NDT) methods, making it challenging to find various other problems or discontinuities within the weld. This can result in considerable safety problems, especially in vital applications where the architectural integrity of the bonded parts is critical.

Avoidance Techniques Summary
Given the destructive impact of porosity on weld top quality, reliable prevention methods are crucial to maintaining the architectural honesty of bonded joints. In addition, picking the appropriate welding criteria, such as voltage, current, and travel rate, can aid decrease the threat of porosity development. By incorporating these avoidance strategies into welding practices, the occurrence of porosity can be significantly lowered, leading to more powerful and much more dependable welded joints.
Value of Proper Shielding
Appropriate protecting in welding plays a vital duty in preventing climatic contamination and making sure the integrity of bonded joints. Protecting gases, such as argon, helium, or a combination of both, are typically used to shield the weld swimming pool from reacting with components airborne like oxygen and nitrogen. When these reactive elements come right into contact with the hot weld pool, they can trigger porosity, resulting in weak welds with lowered mechanical residential properties.
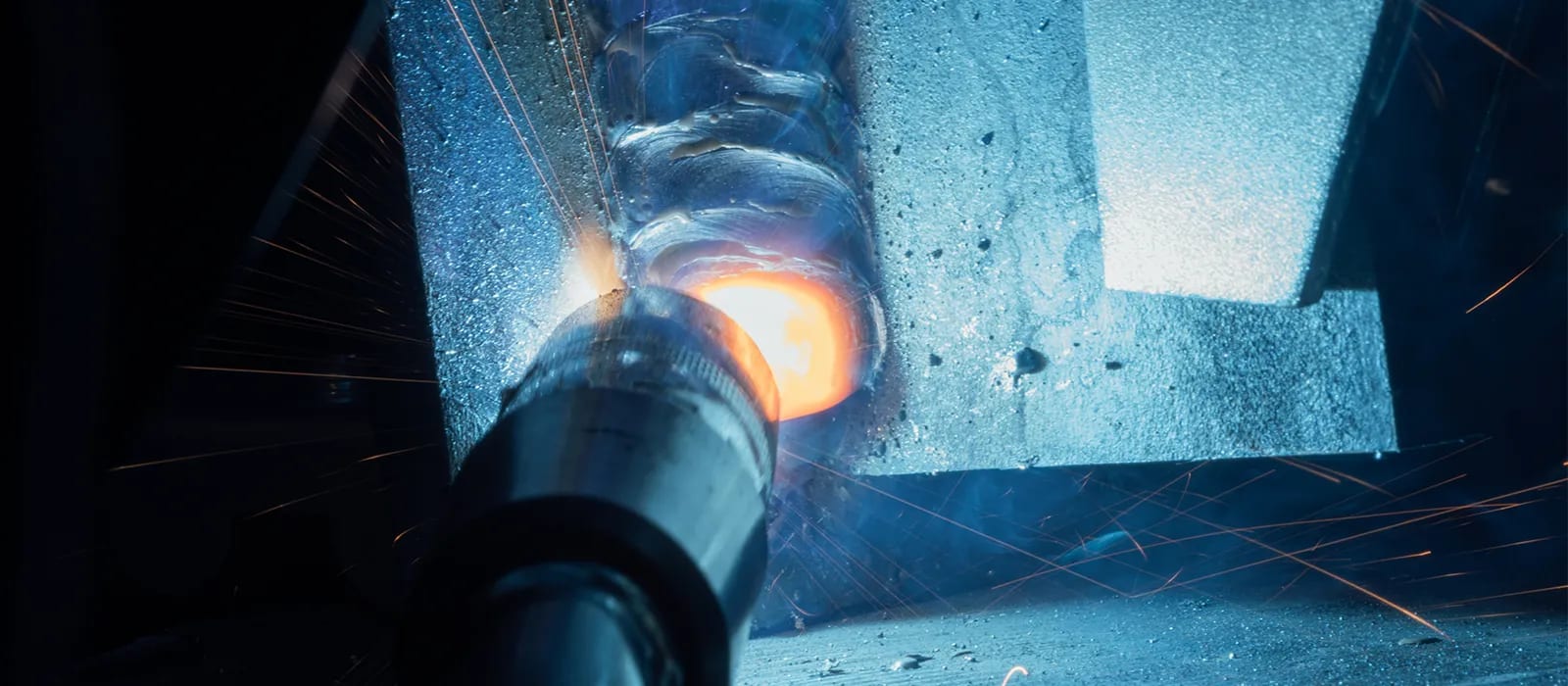
Inadequate shielding can lead to numerous flaws like porosity, spatter, and oxidation, jeopardizing the structural stability of the bonded joint. Sticking to appropriate securing practices is crucial to generate high-quality welds with minimal flaws and ensure the long life and reliability of the bonded components.
Tracking and Control Techniques
How can welders effectively check and regulate the welding procedure to guarantee optimum results and prevent problems like porosity? One secret method is through the usage of innovative monitoring modern technologies. These can include real-time tracking systems that provide feedback on specifications such as voltage, existing, take a trip rate, and gas circulation rates. By continually monitoring these variables, welders can identify inconsistencies from the optimal problems and make prompt modifications to avoid porosity development.

In addition, implementing appropriate training programs for welders is vital for keeping an eye on and managing the welding procedure effectively. What is Porosity. Informing welders on the value of preserving consistent parameters, such as proper browse this site gas protecting and travel speed, can assist avoid porosity problems. Regular assessments and qualifications can likewise ensure that welders are skillful in tracking and managing welding procedures
In addition, using automated welding systems can enhance tracking and control capacities. These systems can specifically regulate welding criteria, lowering the probability of human mistake and making sure consistent weld top quality. By incorporating advanced monitoring innovations, reference training programs, and automated systems, welders can successfully monitor and regulate the welding process to decrease porosity flaws and achieve premium welds.
Final Thought
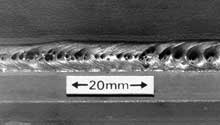
Report this page